A drill grinding machine is a tool used to sharpen and restore the cutting edges of drill bits to ensure precise and efficient drilling. It is commonly used in workshops, manufacturing, and tool maintenance settings.
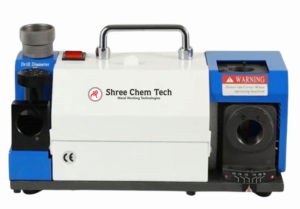
- Quick Re-sharpening of HSS or Carbide drills of taper or straight shank.
- Two separate stations for point angle grinding and relieving.
- Very easy to learn operation by instruction sheet.
- CBN grinding wheel for HSS drills and all size collets included as standard equipment SDC grinding wheel for carbide drill and additional collets are optional.
Model | Drill Dia Capacity | Dia Capacity With Optional Collets | Point Angle Adjustment | Power | N.W.KGS. |
---|---|---|---|---|---|
SDG – 13 | 3 – 13 | 3 – 13 | 90oC – 135oC | AC-220V / 120W | 10 |
SDG – 20 | 3 – 20 | 3 – 20 | 90oC – 135oC | AC-220V / 120W | 11 |
SDG – 26 | 13 – 26 | 8 – 30 | 80oC – 140oC | AC-220V / 250W | 29 |
Benefits
- Cost Savings
- By regrinding dull or worn-out drill bits instead of replacing them, companies can save money on purchasing new tools.
- Extended Tool Life
- Regrinding restores the sharpness and cutting edges of drill bits, allowing them to be used for longer periods before needing replacement.
- Increased Productivity
- Sharp drill bit cut more efficiently, reducing the time required to complete drilling operations and improving overall productivity.
- Improved Quality
- Regrinding ensures that drill bits maintain precise dimensions and cutting geometry, resulting in better quality holes finished
Packing List | ER Collet | Collet Sleeve | Diamond Wheel |
---|---|---|---|
SDG – 13 | 2 – 13 mm | 1 | 1 |
SDG – 20 | 3 – 20 mm | 1 | 1 |
SDG – 30 | 8 – 30 mm | 1 | 1 |